Zablokowanie komórek wałków aniloksowych jest w rzeczywistości najbardziej nieuniknionym problemem podczas korzystania z wałków aniloksowych. Jego objawy dzielą się na dwa przypadki: zablokowanie powierzchni wałka aniloksowego (Postać.1) i zablokowanie komórek wałka aniloksowego (Postać. 2).
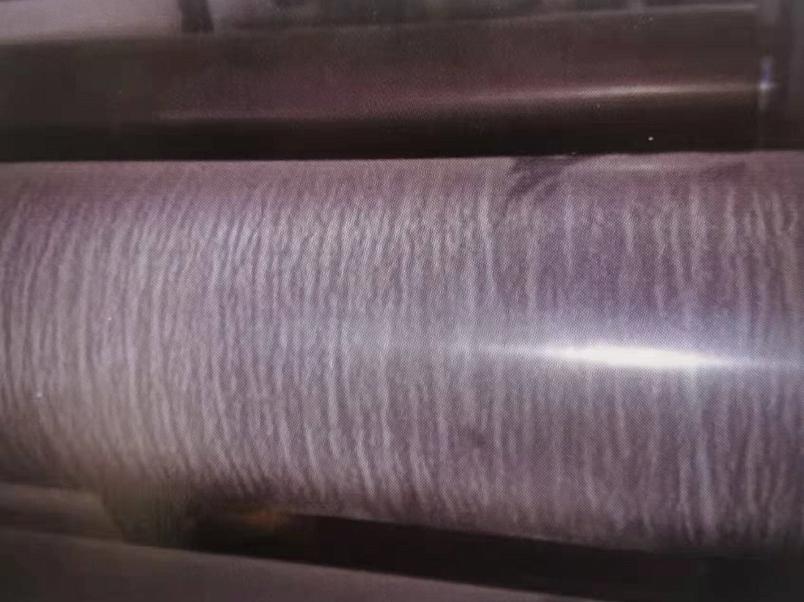
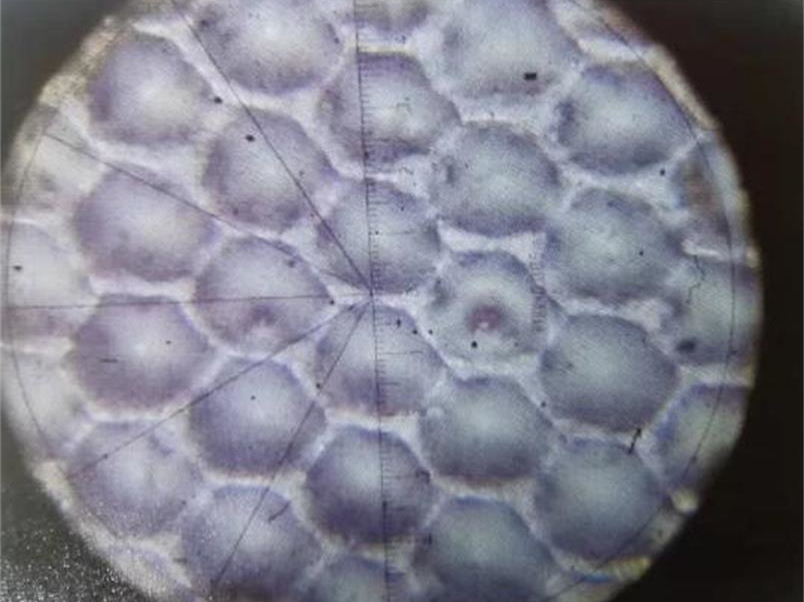
Rysunek 1
Rysunek 2
Typowy system farb fleksograficznych składa się z komory farbowej (zamknięty system podawania farby), wałka aniloksowego, cylindra płyty i podłoża. Konieczne jest ustanowienie stabilnego procesu przenoszenia farby między komorą farbową, komórkami wałka aniloksowego, powierzchnią punktów płyty drukarskiej i powierzchnią podłoża w celu uzyskania wysokiej jakości wydruków. W tej ścieżce przenoszenia farby szybkość przenoszenia farby z wałka aniloksowego na powierzchnię płyty wynosi około 40%. Przenoszenie farby z płyty na podłoże wynosi około 50%. Można zauważyć, że taki transfer farby ścieżką nie jest prostym fizycznym transferem, ale złożonym procesem obejmującym przenoszenie farby, suszenie farby i ponowne rozpuszczanie farby. Wraz ze wzrostem prędkości drukowania maszyny fleksograficznej ten złożony proces nie tylko będzie stawał się coraz bardziej skomplikowany, ale również częstotliwość wahań w transmisji farby ścieżką będzie coraz szybsza; Wymagania dotyczące właściwości fizycznych otworów również stają się coraz wyższe.
Polimery z mechanizmem sieciowania są szeroko stosowane w farbach drukarskich, takich jak poliuretan, żywica akrylowa itp., w celu poprawy przyczepności, odporności na ścieranie, wodoodporności i odporności chemicznej warstwy farby. Ponieważ szybkość transferu farby w komórkach wałka rastrowego wynosi zaledwie 40%, większość farby w komórkach pozostaje na dnie komórek przez cały proces drukowania. Nawet wymiana części farby może spowodować jej wyczerpanie w komórkach. Sieciowanie żywicy zachodzi na powierzchni podłoża, co prowadzi do zatkania komórek wałka rastrowego.
Łatwo zrozumieć, że powierzchnia wałka rastrowego jest zablokowana. Zazwyczaj wałek rastrowy jest nieprawidłowo używany, przez co farba ulega utrwaleniu i usieciowaniu na powierzchni wałka rastrowego, co prowadzi do zablokowania.
Dla producentów wałków rastrowych badania i rozwój technologii powłok ceramicznych, udoskonalenie technologii aplikacji laserowej oraz udoskonalenie technologii obróbki powierzchni ceramicznych po grawerowaniu wałków rastrowych mogą zmniejszyć zatykanie się komór wałków rastrowych. Obecnie powszechnie stosowane metody obejmują zmniejszenie szerokości ścianki siatki, poprawę gładkości wewnętrznej ścianki siatki oraz poprawę zwartości powłoki ceramicznej.
W przypadku przedsiębiorstw drukarskich można także dostosować prędkość schnięcia farby, jej rozpuszczalność i odległość od punktu rakli do punktu drukowania, aby zmniejszyć ryzyko zatkania się komór wałka aniloksowego.
Korozja
Korozja odnosi się do zjawiska punktowych wypustek na powierzchni wałka aniloksowego, jak pokazano na rysunku 3. Korozję powoduje środek czyszczący, który wnika w dolną warstwę wzdłuż szczeliny ceramicznej, powodując korozję dolnego metalowego wałka bazowego i pękanie warstwy ceramicznej od wewnątrz, co powoduje uszkodzenie wałka aniloksowego (rysunek 4, rysunek 5).
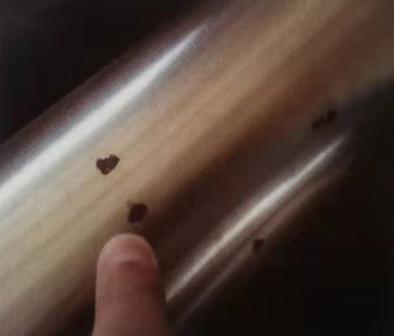
Rysunek 3
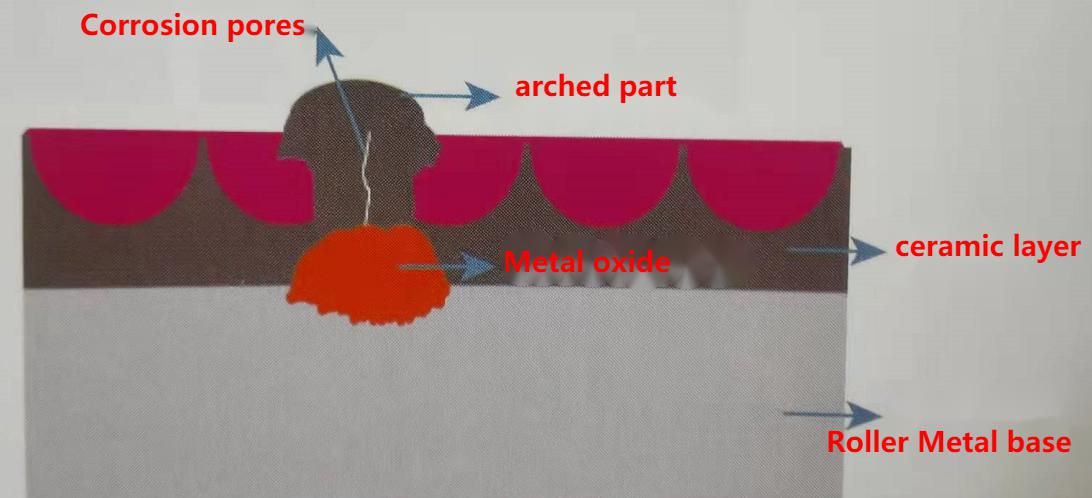
Rysunek 4
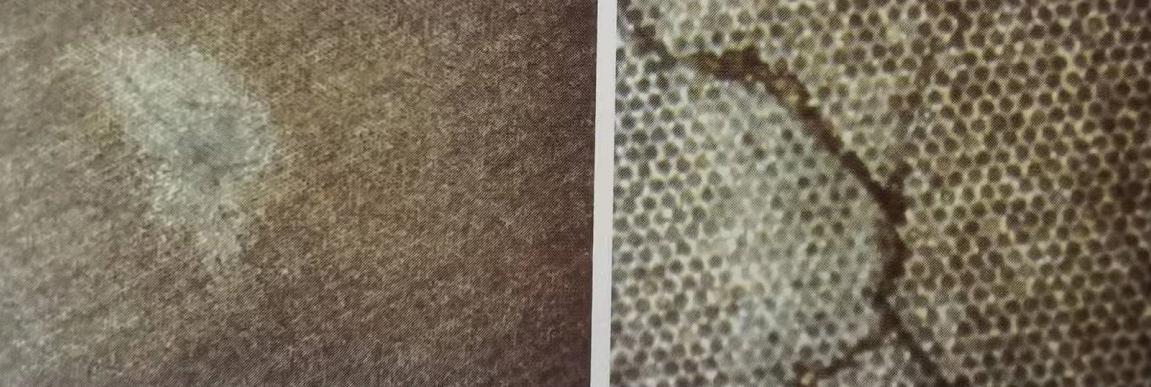
Rysunek 5. Korozja pod mikroskopem
Przyczynami powstawania korozji są:
① Pory powłoki są duże, a ciecz może przedostać się przez nie do wałka dolnego, powodując korozję wałka dolnego.
② Długotrwałe stosowanie środków czyszczących, takich jak silne kwasy i silne zasady, bez odpowiedniego prysznica i suszenia na powietrzu po użyciu.
③ Metoda czyszczenia jest nieprawidłowa, zwłaszcza w przypadku długotrwałego czyszczenia sprzętu.
④ Metoda przechowywania jest nieprawidłowa, produkt był przechowywany w wilgotnym środowisku przez długi czas.
⑤ Wartość pH tuszu lub dodatków jest zbyt wysoka, zwłaszcza tuszu na bazie wody.
⑥ Podczas montażu i demontażu dochodzi do uderzeń w wałek aniloksowy, co powoduje zmianę szczeliny między warstwą ceramiczną.
Początkowa operacja jest często pomijana ze względu na długi czas między wystąpieniem korozji a ostatecznym uszkodzeniem wałka rastrowego. Dlatego po stwierdzeniu zjawiska „workowania” ceramicznego wałka rastrowego, należy skontaktować się z dostawcą ceramicznych wałków rastrowych w celu zbadania przyczyny powstawania łuku.
Zadrapania obwodowe
Zarysowania wałków aniloksowych są najczęstszym problemem wpływającym na żywotność wałków aniloksowych.(rysunek 6)Dzieje się tak, ponieważ cząsteczki znajdujące się między wałkiem rastrowym a raklami, pod wpływem nacisku, rozbijają powierzchnię ceramiki wałka rastrowego i otwierają wszystkie ścianki siatki w kierunku drukowania, tworząc rowek. Efektem końcowym wydruku jest ciemniejsze linie.
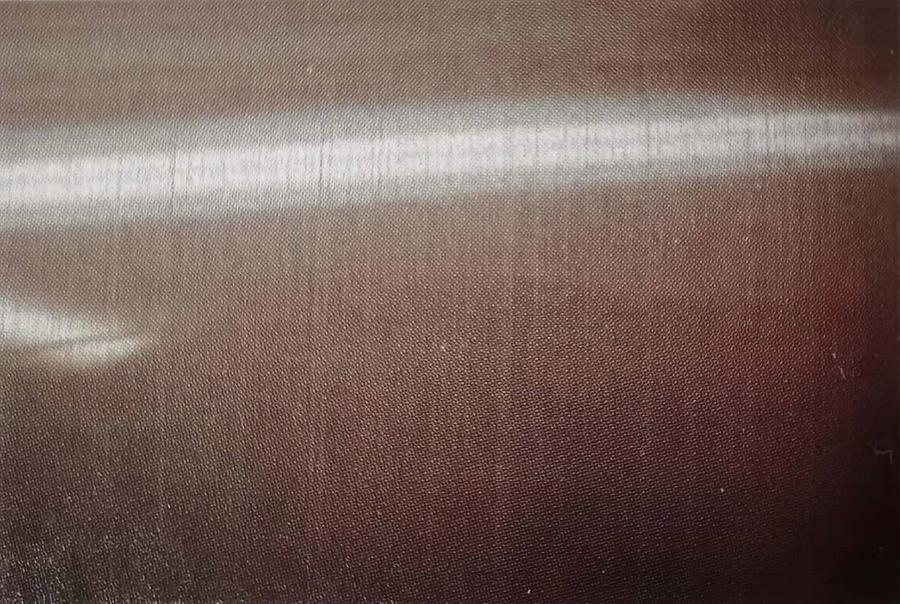
Rysunek 6. Wałek aniloksowy z zarysowaniami
Głównym problemem związanym z zarysowaniami jest zmiana nacisku między listwą raklową a wałkiem rastrowym, wskutek czego pierwotny nacisk czołowy staje się lokalnym naciskiem czołowym. Ponadto duża prędkość drukowania powoduje gwałtowny wzrost nacisku, a siła niszcząca jest zadziwiająca (rysunek 7).
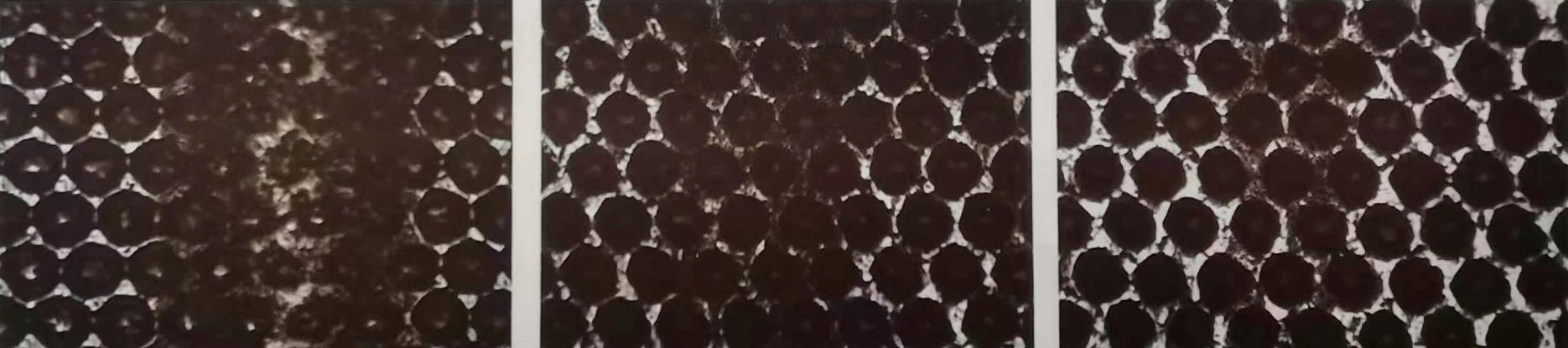
Rysunek 7 - poważne zadrapania
Ogólne zadrapania
drobne rysy
Zazwyczaj, w zależności od prędkości drukowania, zarysowania, które wpływają na druk, powstają w ciągu 3 do 10 minut. Na ten nacisk wpływa wiele czynników, głównie takich jak: sam wałek raklowy, czyszczenie i konserwacja systemu rakla, jakość, montaż i użytkowanie rakla oraz wady konstrukcyjne sprzętu.
1. sam wałek aniloksowy
(1) Obróbka powierzchni ceramicznego wałka aniloksowego po grawerowaniu nie jest wystarczająca, a powierzchnia jest szorstka i łatwo ją zarysować skrobakiem i ostrzem skrobaka.
Powierzchnia styku z wałkiem rastrowym uległa zmianie, co spowodowało wzrost nacisku, jego zwielokrotnienie i przerwanie siatki podczas pracy z dużą prędkością.
Na powierzchni wałka tłoczonego tworzą się zarysowania.
(2) Podczas procesu polerowania i szlifowania precyzyjnego powstaje głęboka linia polerowania. Taka sytuacja zazwyczaj ma miejsce po dostarczeniu wałka aniloksowego, a lekko wypolerowana linia nie wpływa na druk. W takim przypadku weryfikacja druku musi zostać przeprowadzona na maszynie.
2. czyszczenie i konserwacja układu rakla
(1) Niezależnie od tego, czy poziom listwy raklowej komory jest skorygowany, listwa raklowa komory z nieprawidłowym poziomem będzie powodować nierównomierne ciśnienie. (rysunek 8)
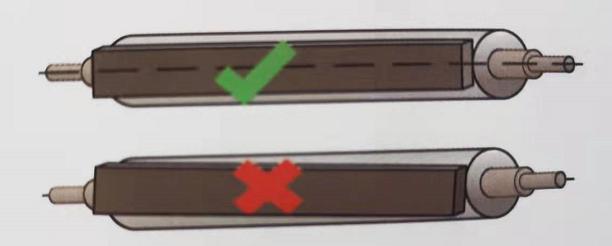
Rysunek 8
(2) Niezależnie od tego, czy komora rakla jest utrzymywana w pozycji pionowej, komora atramentowa w pozycji niepionowej zwiększy powierzchnię styku rakla. W rzeczywistości może to bezpośrednio uszkodzić wałek raklowy. Rysunek 9
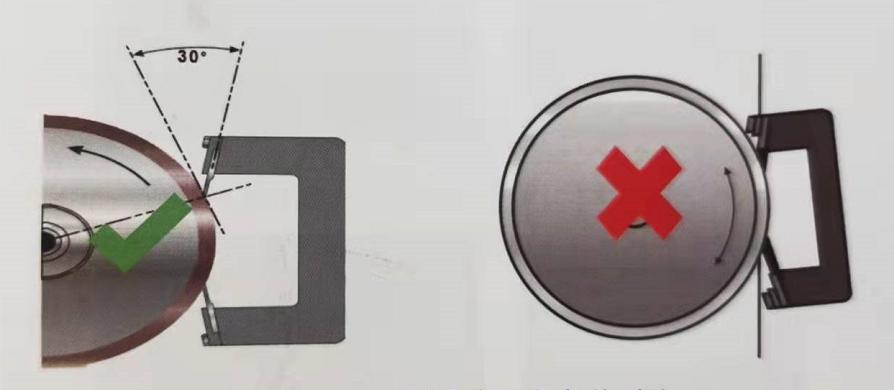
Rysunek 9
(3) Czyszczenie systemu rakla komory jest bardzo ważne. Zapobiega przedostawaniu się zanieczyszczeń do układu atramentowego, które mogłyby utknąć między raklami a wałkiem rastrowym, powodując zmiany ciśnienia. Wyschnięty tusz jest również bardzo niebezpieczny.
3. Montaż i użytkowanie listwy raklowej
(1) Prawidłowo zamontuj listwę raklową komory, aby mieć pewność, że listwa nie ulegnie uszkodzeniu, będzie prosta, bez fal i idealnie dopasowana do uchwytu listwy, np.
Jak pokazano na rysunku 10, należy upewnić się, że nacisk na powierzchnię wałka aniloksowego jest równomierny.
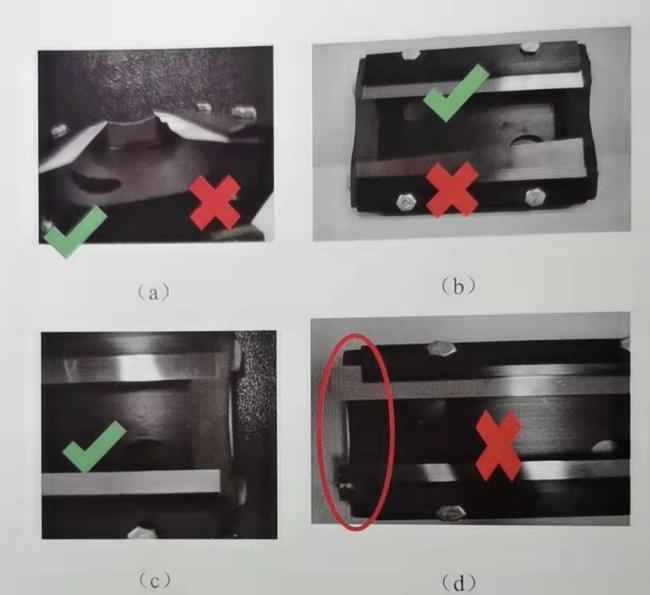
Rysunek 10
(2) Używaj skrobaków wysokiej jakości. Wysokiej jakości stal skrobakowa ma zwartą strukturę molekularną, jak pokazano na rysunku 11 (a), po zużyciu. Cząsteczki są małe i jednorodne; struktura molekularna niskiej jakości stali skrobakowej nie jest wystarczająco zwarta, a cząstki są duże po zużyciu, jak pokazano na rysunku 11 (b).
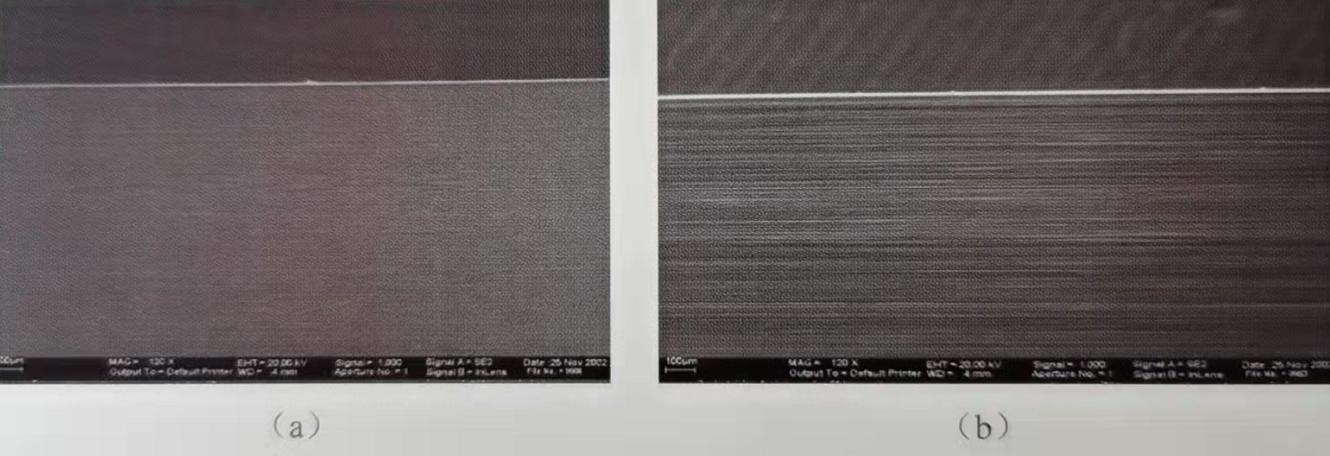
Rysunek 11
(3) Wymieniaj nóż z ostrzem na czas. Podczas wymiany zwróć uwagę, aby chronić krawędź noża przed uderzeniem. Podczas zmiany numeru linii wałka aniloksowego należy wymienić nóż z ostrzem. Stopień zużycia wałka aniloksowego o różnych numerach linii jest niespójny, jak pokazano na rysunku 12, lewy rysunek przedstawia ekran o niskim numerze linii Szlifowanie noża z ostrzem na nożu z ostrzem Stan uszkodzonej powierzchni końcowej, rysunek po prawej stronie przedstawia stan zużytej powierzchni końcowej wałka aniloksowego o wysokiej liczbie linii do noża z ostrzem. Powierzchnia styku między listwą raklową a wałkiem aniloksowym o niedopasowanych poziomach zużycia zmienia się, powodując zmiany nacisku i zarysowania.
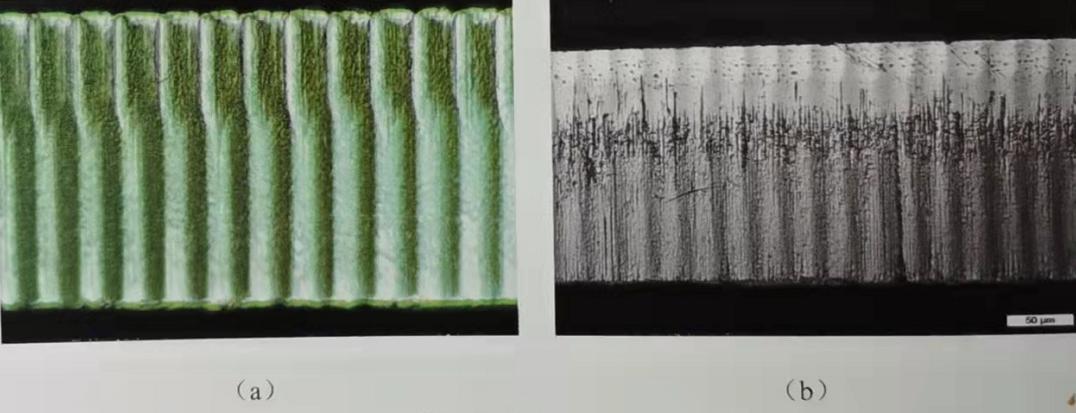
Rysunek 12
(4) Nacisk rakla powinien być niewielki. Nadmierny nacisk rakla zmieni powierzchnię styku i kąt nachylenia rakla i wałka raklowego, jak pokazano na rysunku 13. Łatwo jest wciągać zanieczyszczenia, które po zmianie nacisku powodują zarysowania. Przy nieodpowiednim nacisku na wymieniony skrobak pojawią się zużyte metalowe końcówki (rysunek 14). Po odpadnięciu skrobak wpada między skrobak a wałek raklowy, co może spowodować zarysowania na wałku raklowym.
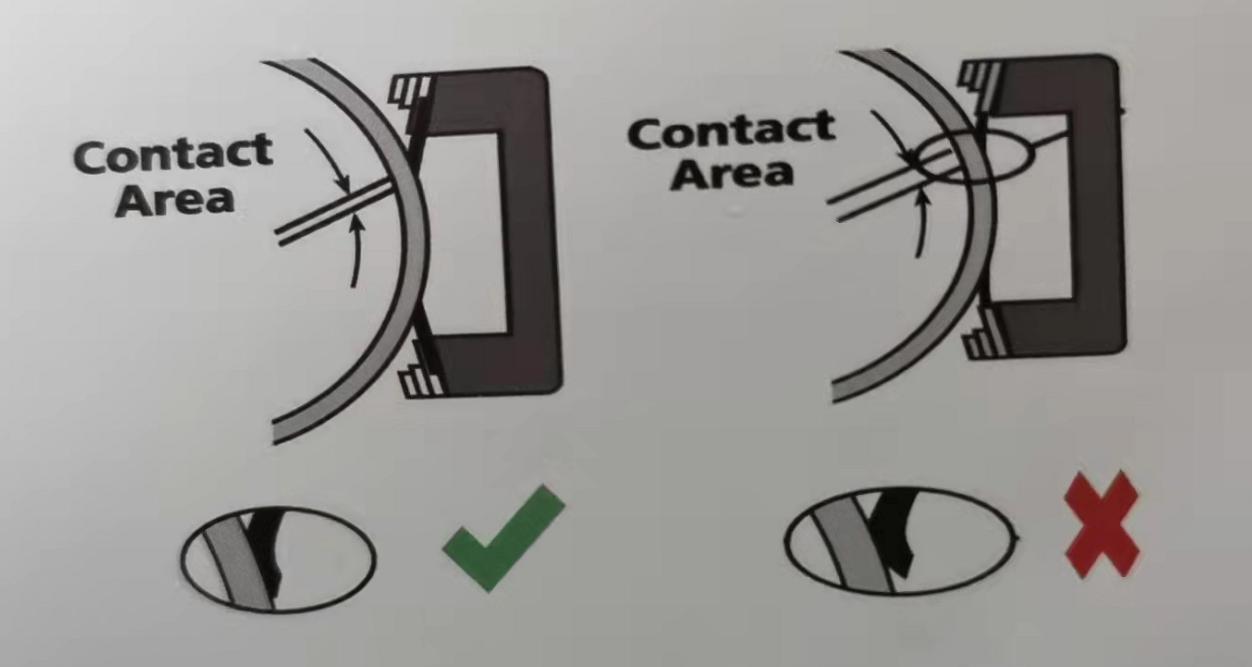
Rysunek 13
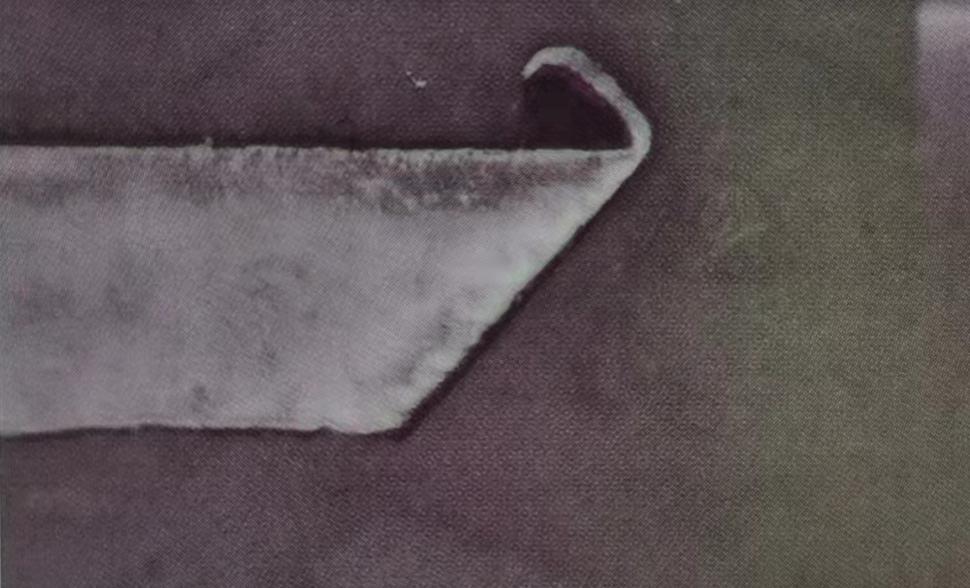
Rysunek 14
4. wady konstrukcyjne sprzętu
Wady konstrukcyjne, takie jak niedopasowanie konstrukcji bloku farbowego do średnicy wałka rastrowego, mogą również powodować łatwe powstawanie zarysowań. Niewłaściwe ustawienie rakla, niedopasowanie średnicy do długości wałka rastrowego itp. będą prowadzić do powstania niepewnych czynników. Widać wyraźnie, że problem zarysowań w kierunku obwodowym wałka rastrowego jest bardzo złożony. Zwracanie uwagi na zmiany ciśnienia, regularne czyszczenie i konserwacja, dobór odpowiedniego skrobaka oraz dobre i uporządkowane nawyki obsługi mogą znacznie ograniczyć problem zarysowań.
Kolizja
Chociaż ceramika charakteryzuje się wysoką twardością, jest materiałem kruchym. Pod wpływem siły zewnętrznej łatwo odpada, tworząc wżery (rysunek 15). Zazwyczaj podczas ładowania i rozładowywania wałków rastrowych występują uderzenia, a metalowe narzędzia spadają z powierzchni wałka. Należy dbać o czystość w miejscu drukowania i unikać gromadzenia się małych przedmiotów wokół maszyny drukarskiej, zwłaszcza w pobliżu tacy z farbą i wałka rastrowego. Zaleca się dokładne czyszczenie wałka rastrowego. Prawidłowe zabezpieczenie wałka zapobiega spadaniu i uderzaniu małych przedmiotów w wałek rastrowy. Podczas ładowania i rozładowywania wałka rastrowego zaleca się owinięcie go elastyczną osłoną ochronną przed użyciem.
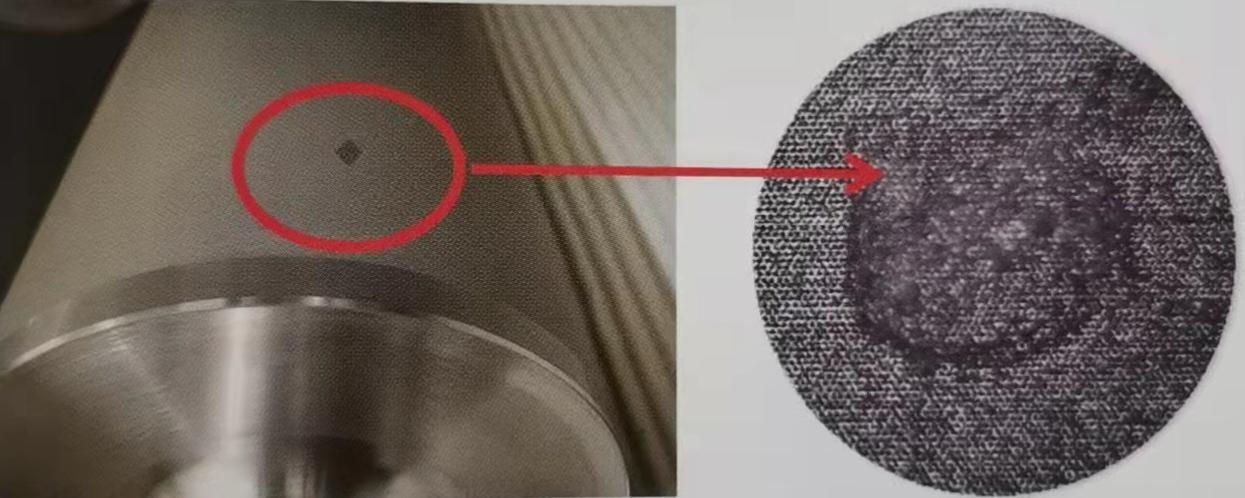
Rysunek 15
Czas publikacji: 23-02-2022